


More Options
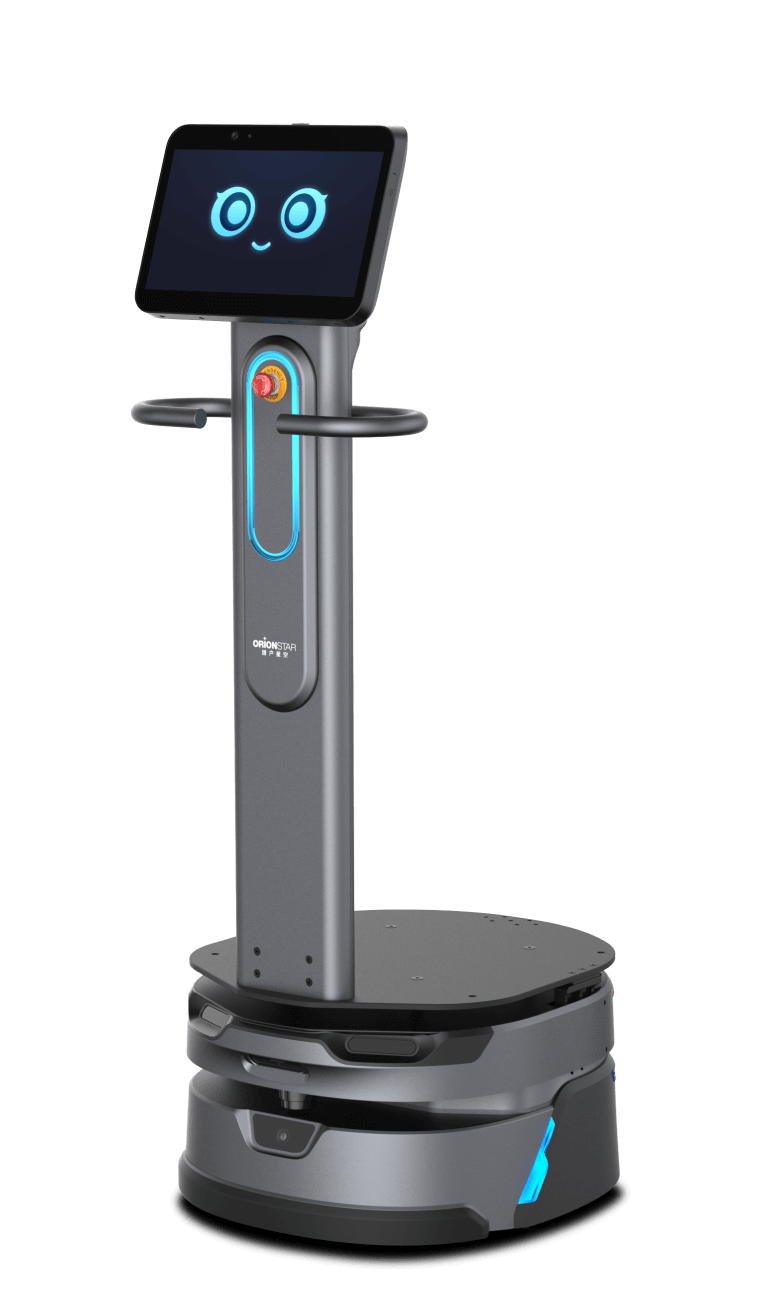
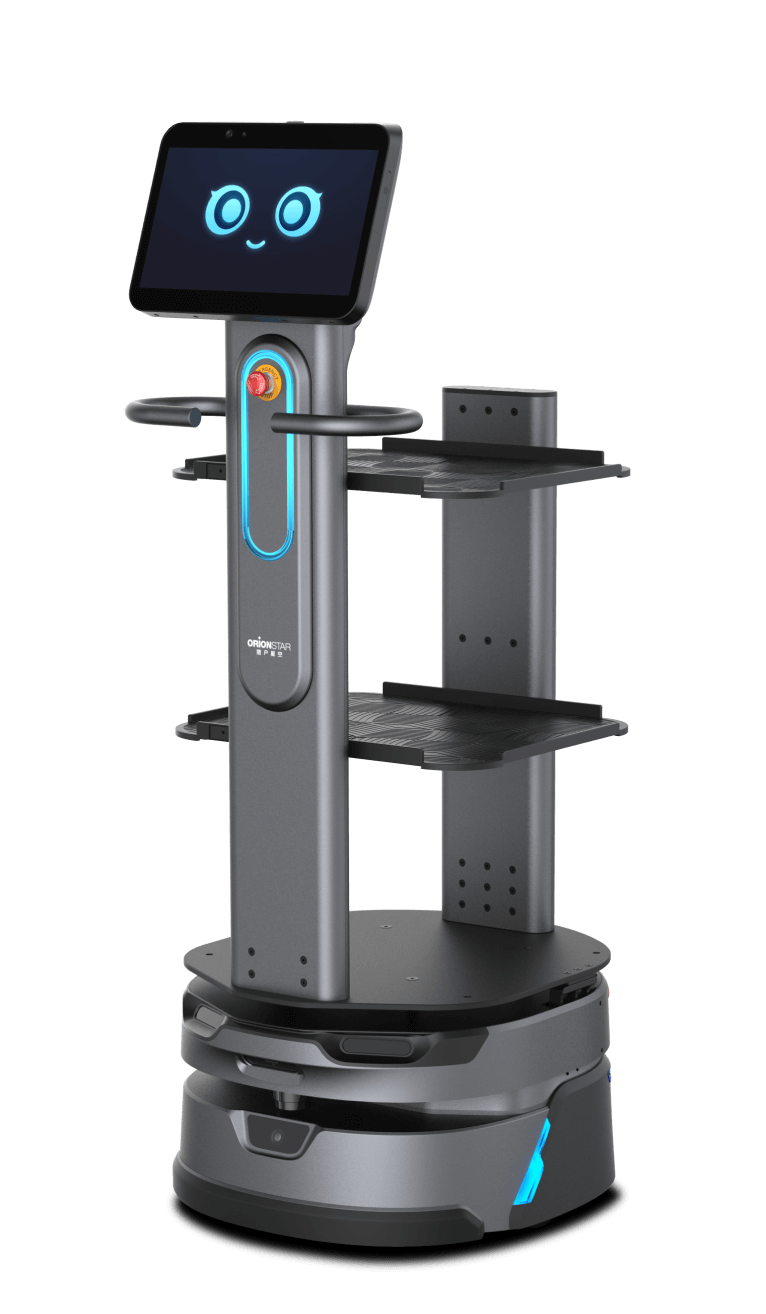
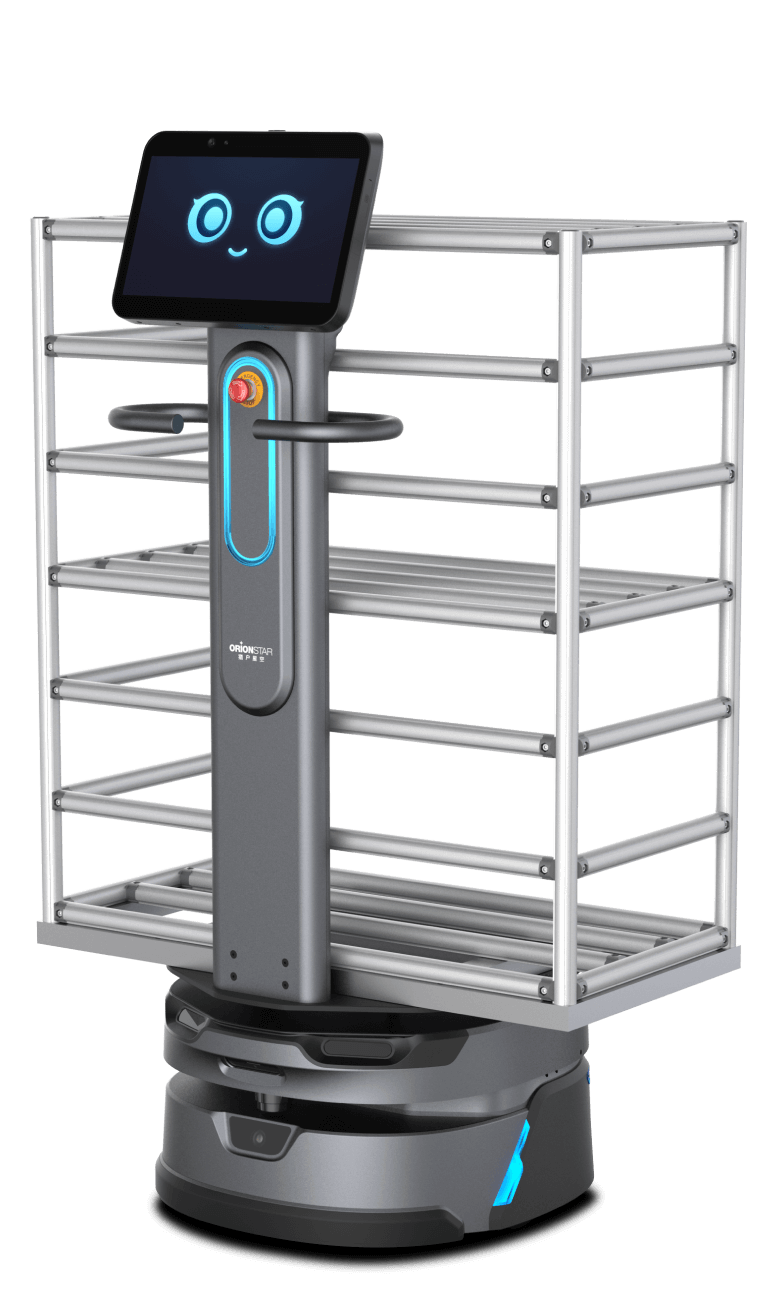
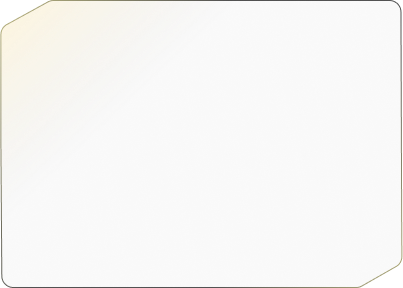
F lexible
· Suitable for 20+ scenarios
· VSLAM + autonomous navigation
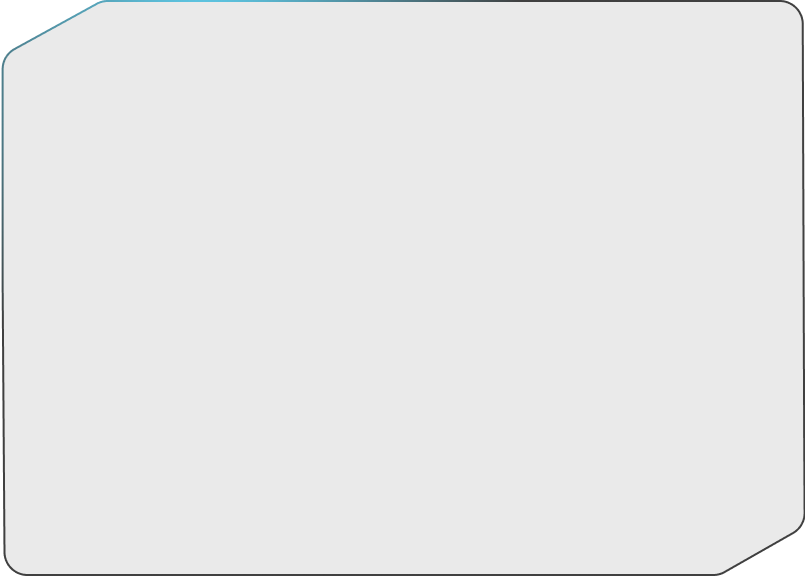
I ntelligent
· Smart summon solution and follow-me mode
· Easy operation with a 14-inch large screen
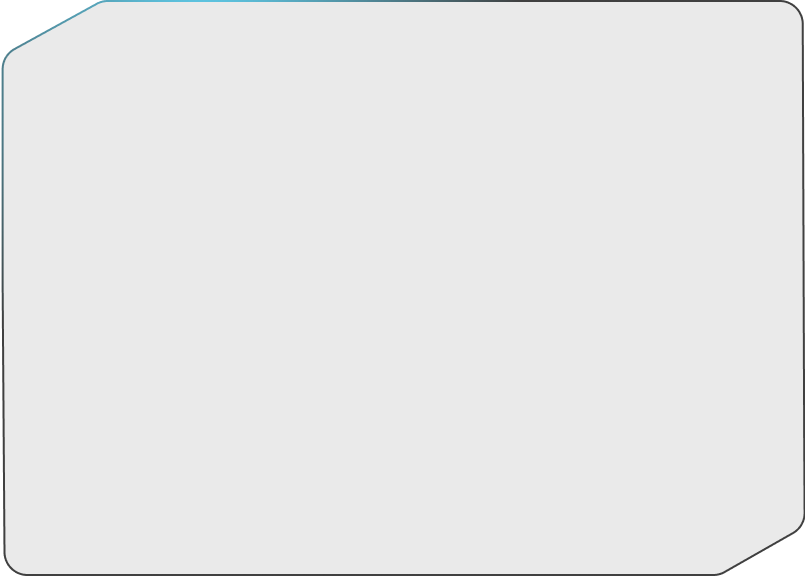
r apid
· Single-robot mapping, intelligent sharing
· No PC is required for deployment
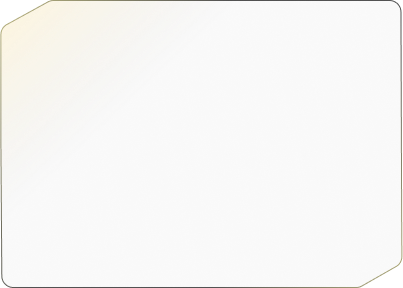
S table
Accuracy
· Service-oriented organization
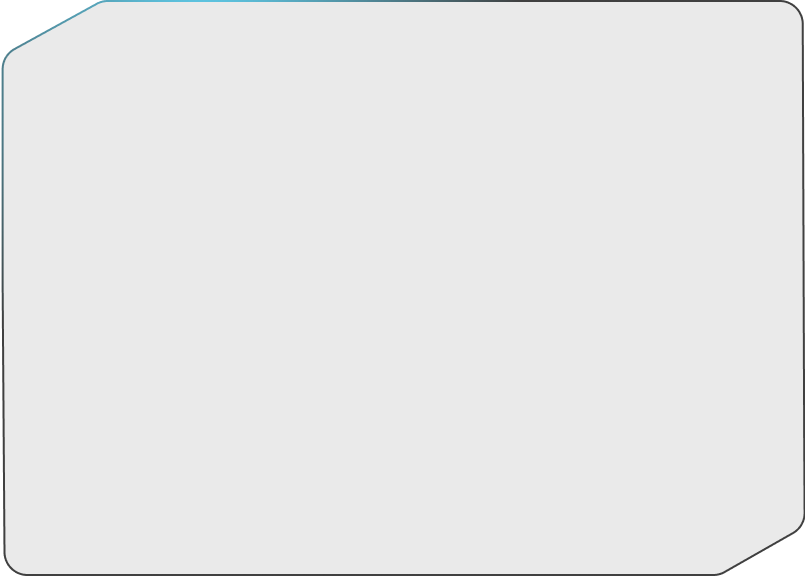
O pen
Robot System
· 3 hardware expansion interfaces
· Average 7-day custom development
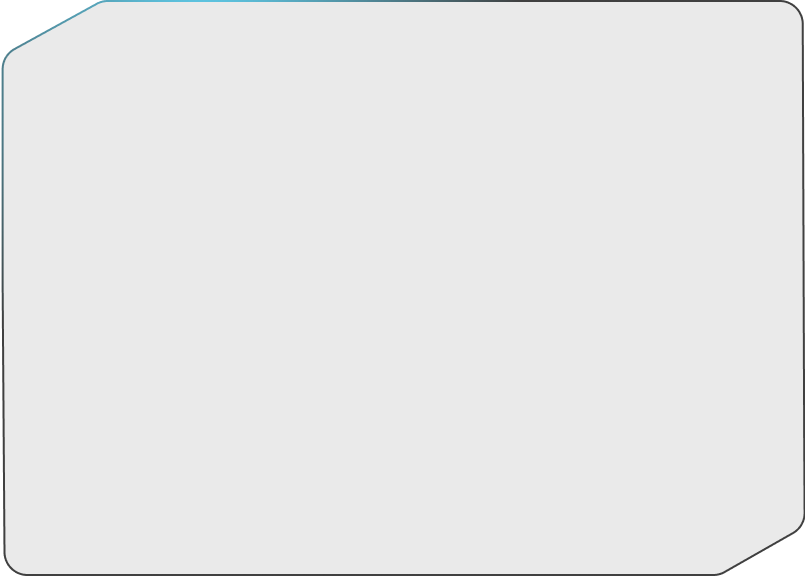
C ollaborative
Collaboration
· 65 cm minimum clearance
· 3-6 times increase in efficiency
![$lock['title']](https://www.orionstar.com/res/orics/down/ow001_20240909_8d58eb841d74479ed93aa05459e2289a.png)
![$lock['title']](https://www.orionstar.com/res/orics/down/ow001_20240909_642bf2b1bc338d96a56bf25ea32f1c59.png)
![$lock['title']](https://www.orionstar.com/res/orics/down/ow001_20240909_0cb319dabe59735a234470e956ee9cd3.png)
![$lock['title']](https://www.orionstar.com/res/orics/down/ow001_20240909_e08cbcddb7ba7e772d3b201576cd1057.png)
![$lock['title']](https://www.orionstar.com/res/orics/down/ow001_20240909_3ec5a526fef6f9ad3b46a1034f50c059.png)
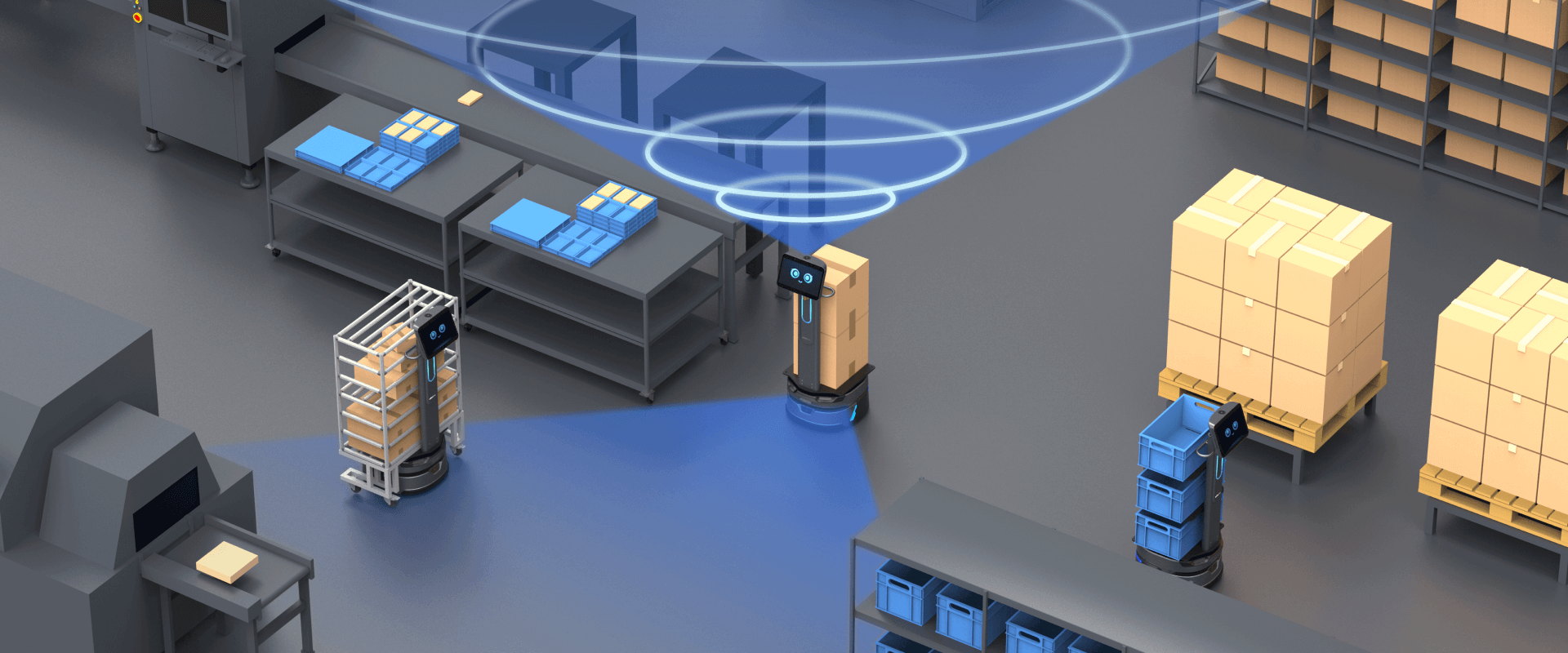
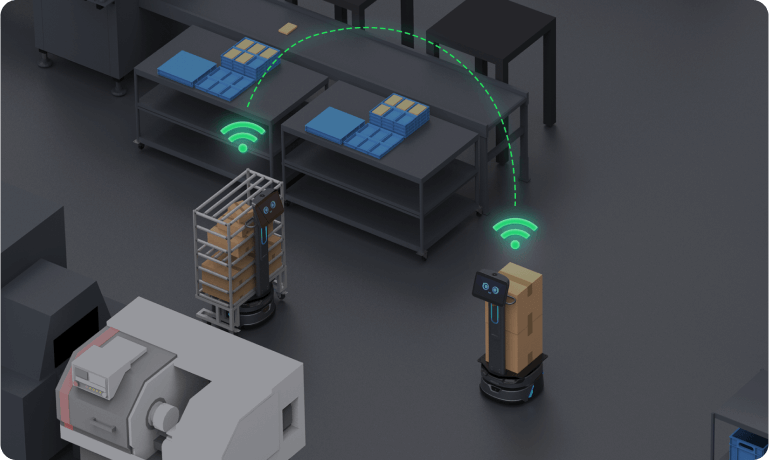
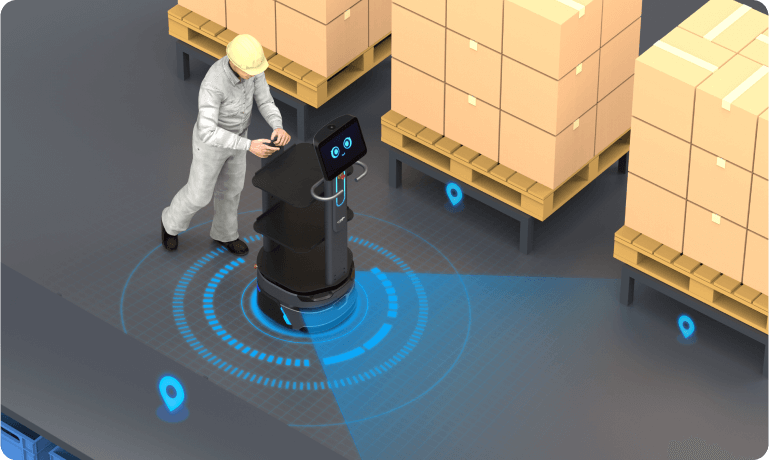
Deployment time is reduced from several weeks with traditional AGVs to less than one day.
With integrated mapping software and no PC required, efficiency is triple.
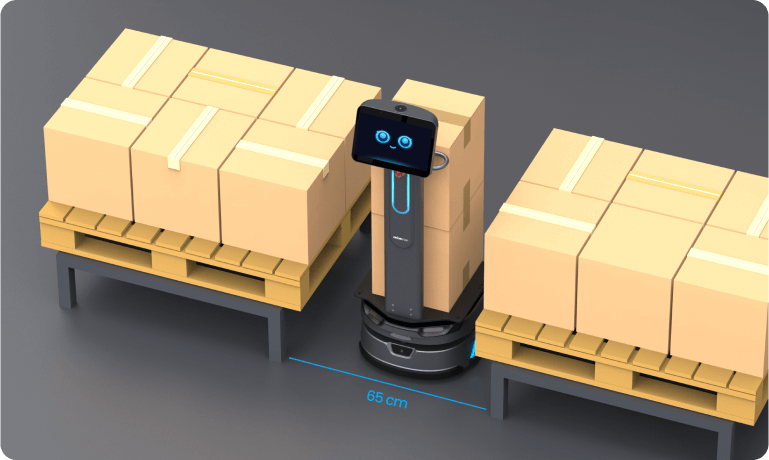
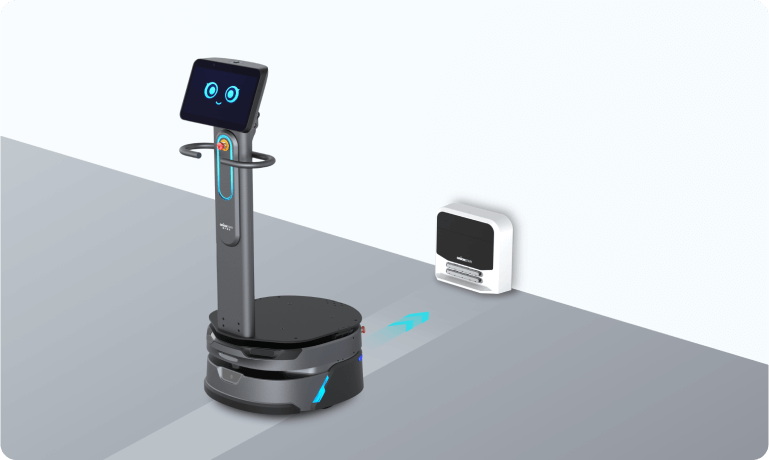
Resume work swiftly: the robot achieves a full charge within 4.5 hours.





CarryBot Solutions
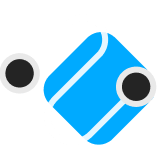
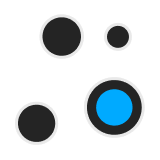
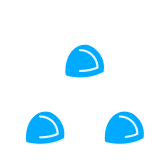
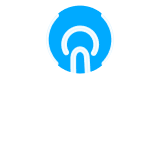
Multi-scenario application
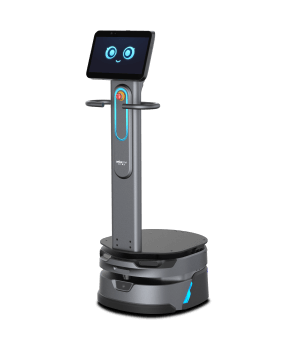
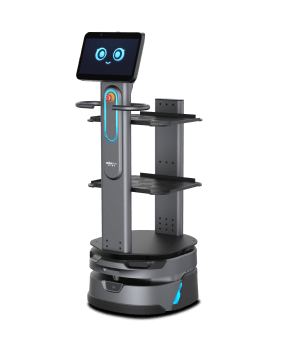
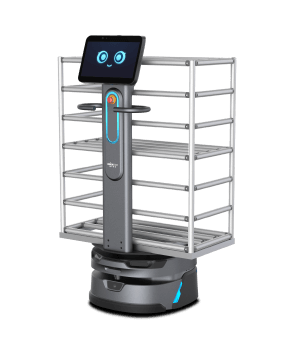
Shelf: 405 mm x 825 mm x 937 mm
Max load: 150 kg (including trays)
More Options
CarryBot-D100
For standard delivery needs, consider the CarryBot D100 – the classic model with a 100kg payload and 9-hour runtime.
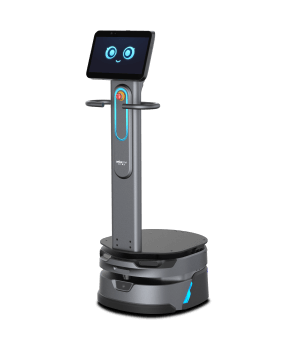
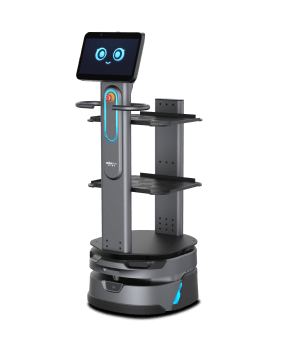
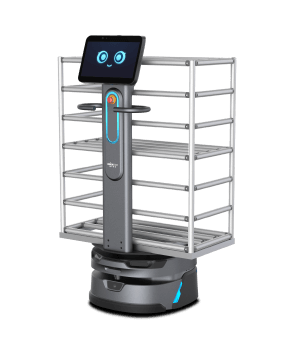
30 kg per tray
(including trays)
30 kg per tray
(including trays)
(including shelf)
(including shelf)
*Note: Tested with a 100 kg load on a marble floor